equipment
Production Machines
Plastic Injection Machine (100T)
100T clamping force injects molten plastic into a precisely machined mold, solidifying it under pressure. The machine’s servo-controlled hydraulic system ensures precise ram movement and injection parameters, guaranteeing consistent product quality. Ideal for complex geometries and high-volume production of plastic parts.
Plastic Injection Machine (180T)
180T clamping force tackles complex geometries and high-volume production. Servo-controlled hydraulics ensure precise melt injection and mold closure for consistent, high-quality plastic parts in applications like automotive, electronics, and medical.
Blow Molding Machine
Molten preform expands within a closed mold under precisely controlled air pressure. The pressurized polymer conforms to the mold’s shape, solidifying as the air cools. Ejection yields hollow plastic objects, ideal for high-volume production of bottles, containers, and toys.
Silicone Injection Machine
Metered silicone injected under controlled pressure into a heated mold. Precise temperature and pressure ensure accurate, defect-free shapes. This versatile machine caters to intricate geometries & diverse silicone types for medical, industrial and consumer applications.
Single Screw Extruder
Within a cylindrical barrel, a rotating screw propels thermoplastic granules. Frictional heat melts them, while the screw geometry channels and mixes the molten polymer. Under pressure, this viscous flow enters a shaped die, defining the final product’s cross-section as it cools and solidifies.
3D Mask Making Machine
Laser melts polymer filament, extruding it layer-by-layer onto a build platform within a controlled thermal environment. Software dictates the precise deposition path, defining the three-dimensional mask geometry. Upon completion, the printed mask undergoes post-processing (e.g., cooling, support removal) and potential sterilization before use.
VMI Strainer
Filters rubber compounds using a gear pump and a single screw extruder. It improves the quality of extruded products by removing impurities and air bubbles from the compound. It can also handle different viscosities and pressures of rubber.
Tube Forming Machine
High-pressure rollers or mandrels deform and weld pre-cut sheet metal into seamless tubes. Precise control of tension, pressure, and forming tools ensures dimensional accuracy and consistent cross-sections. Ideal for high-volume production of tubular components.
Analytical Devices
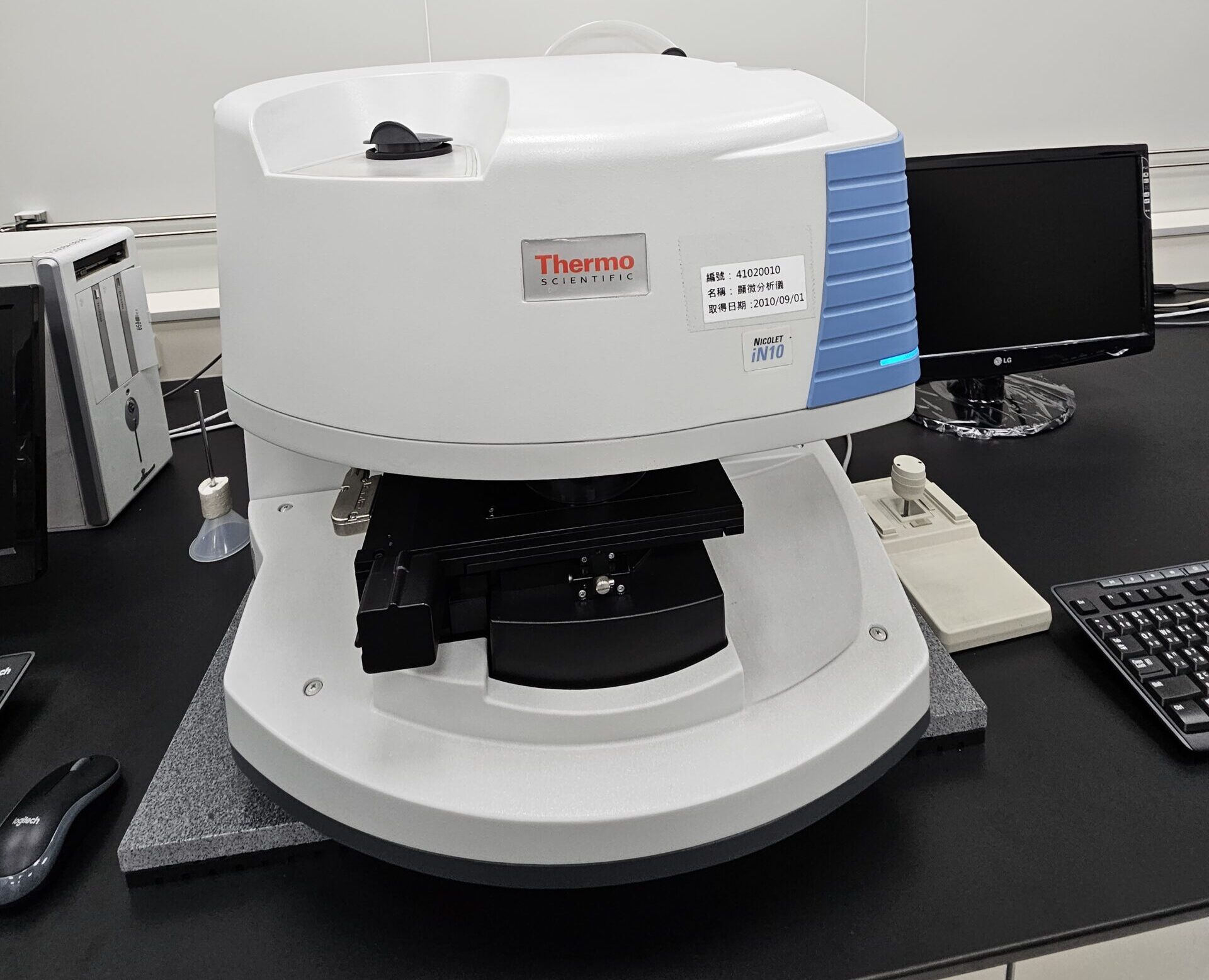
Combines microscope and infrared light to analyze tiny samples like cells and fibers, revealing their chemical makeup.
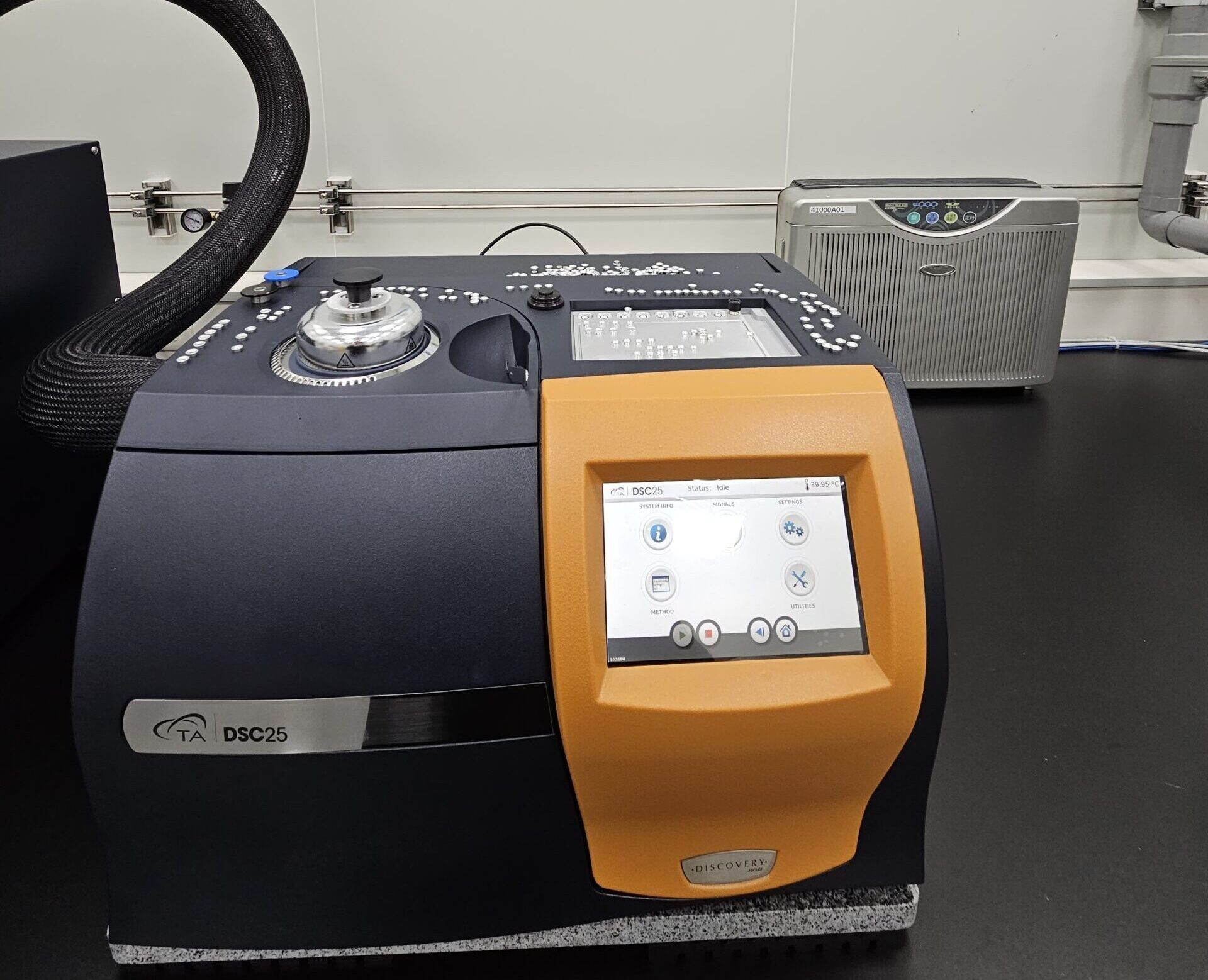
Tracks heat absorbed or released by sample during temperature change, revealing material properties like melting point, mixing compatibility, and chemical reactions.
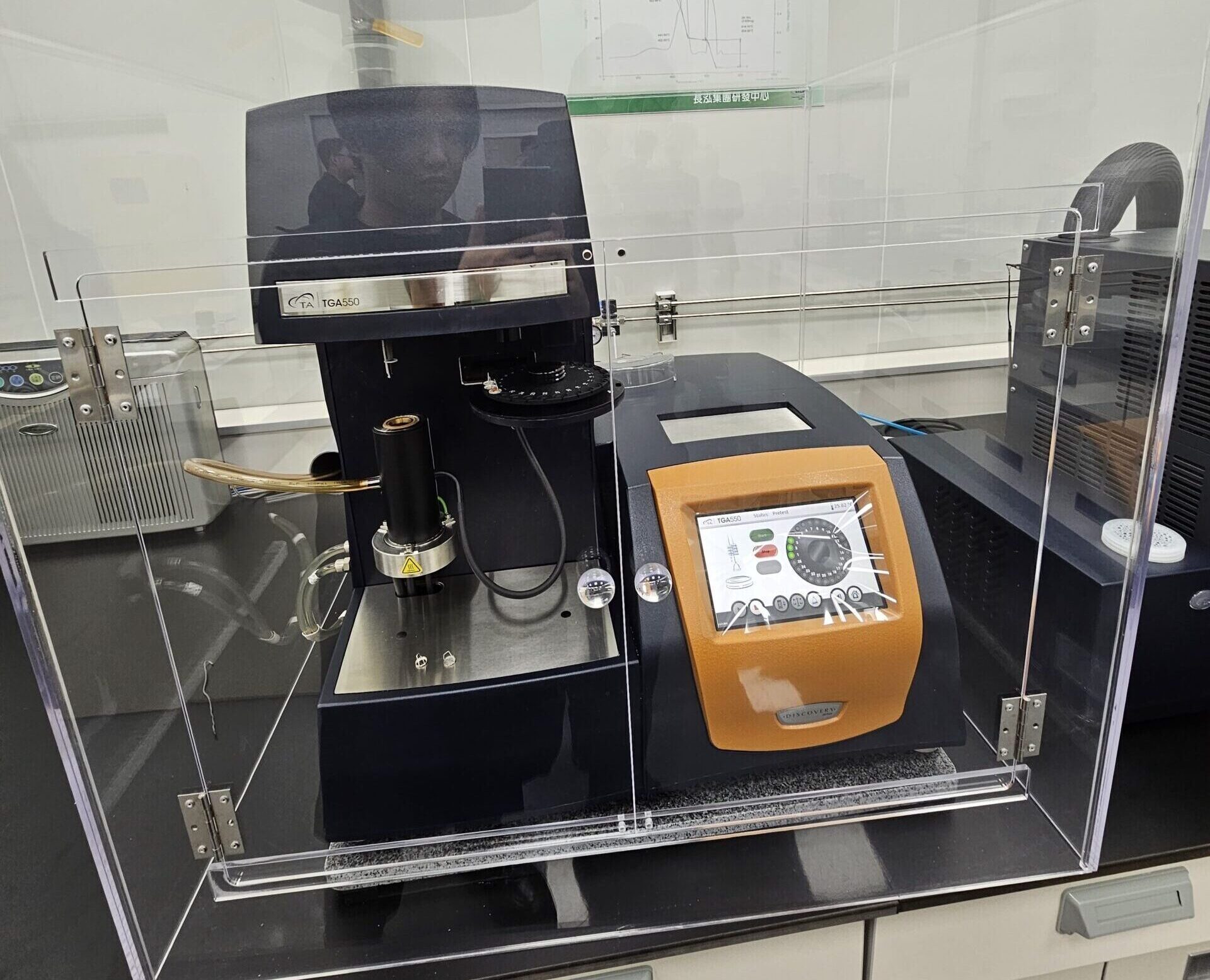
Measures mass change of a sample as temperature and atmosphere vary over time, unveiling decomposition, phase changes, and reaction kinetics as a sample heats up.
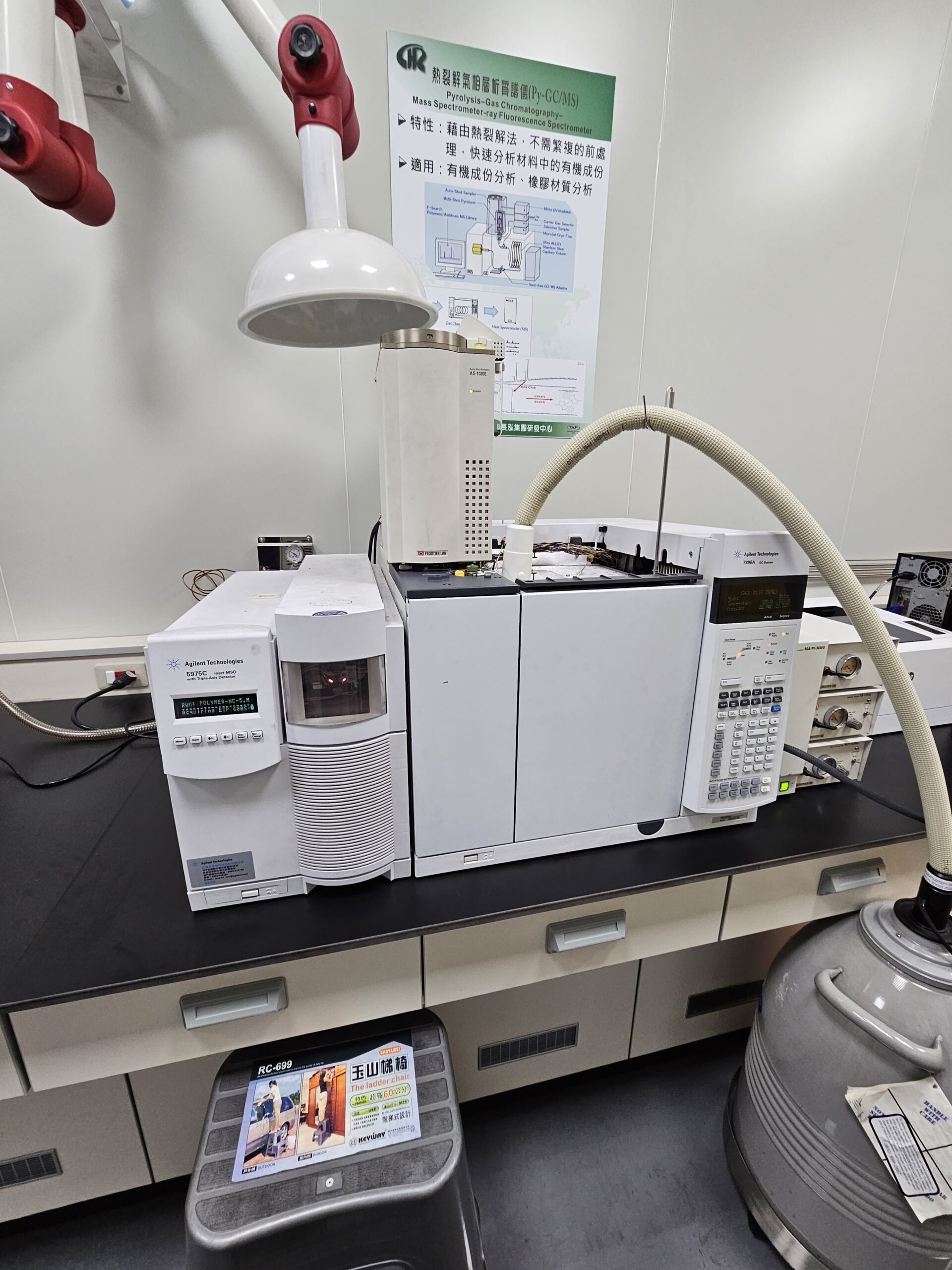
Analyzes materials that decompose when heated. The fragments are separated by gas chromatography and detected by mass spectrometry.
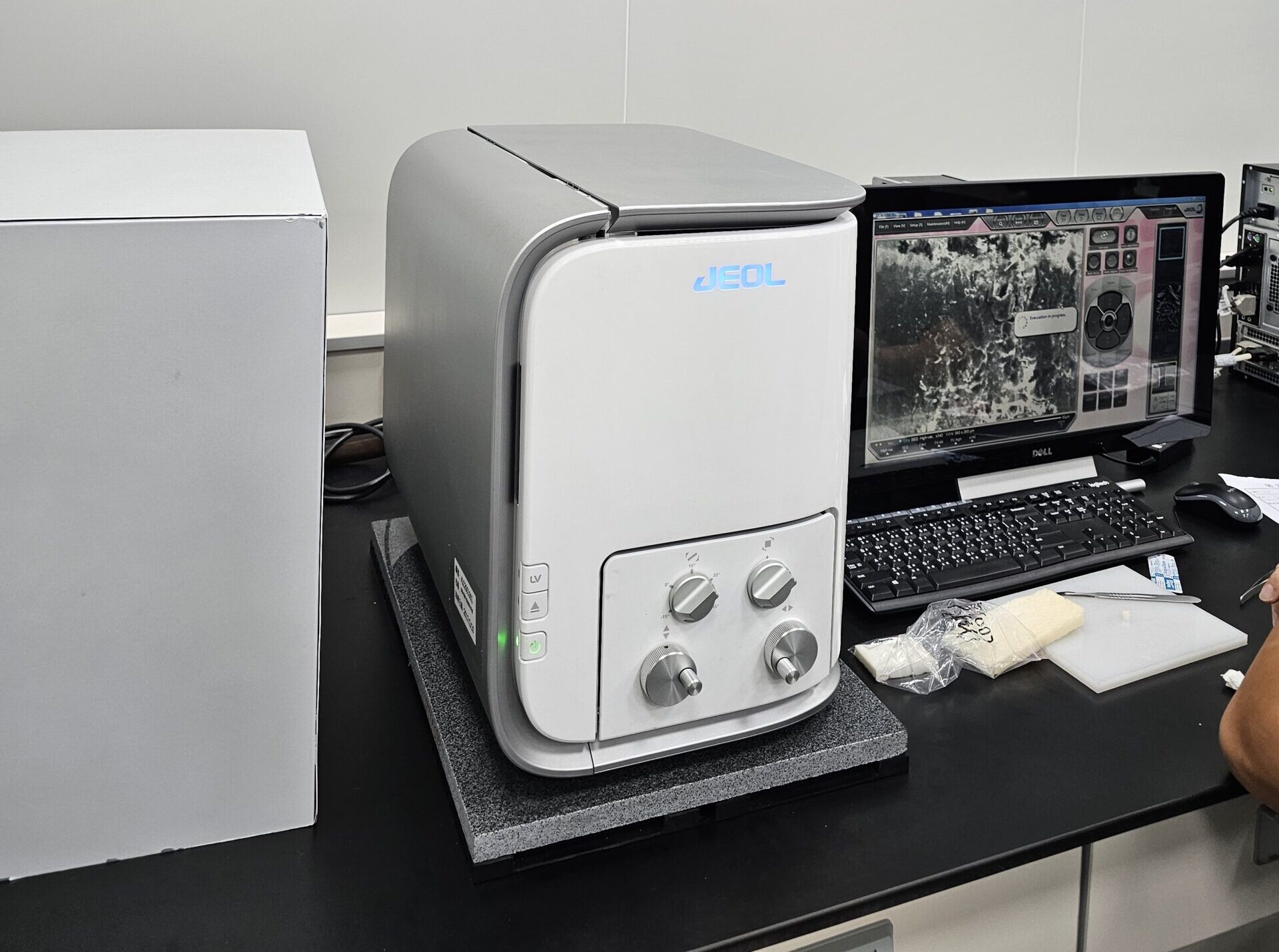
Uses electrons and X-rays to image and analyze materials. SEM provides the imaging, while EDS detects the elements.
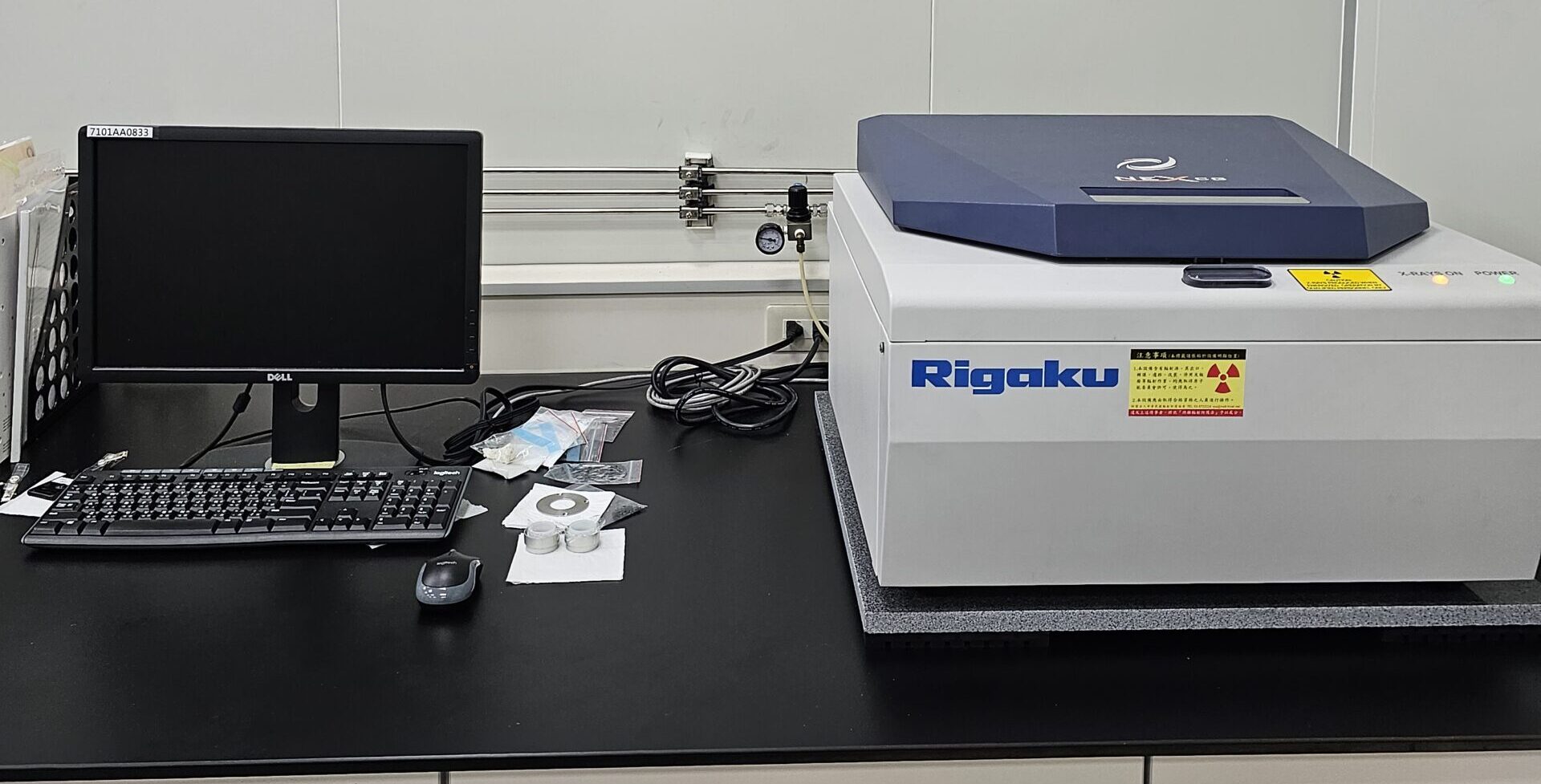
Exposes a sample to a beam of high-energy X-rays or gamma rays, which causes the atoms in the sample to emit fluorescent X-rays with characteristic energies, revealing elemental composition of materials.
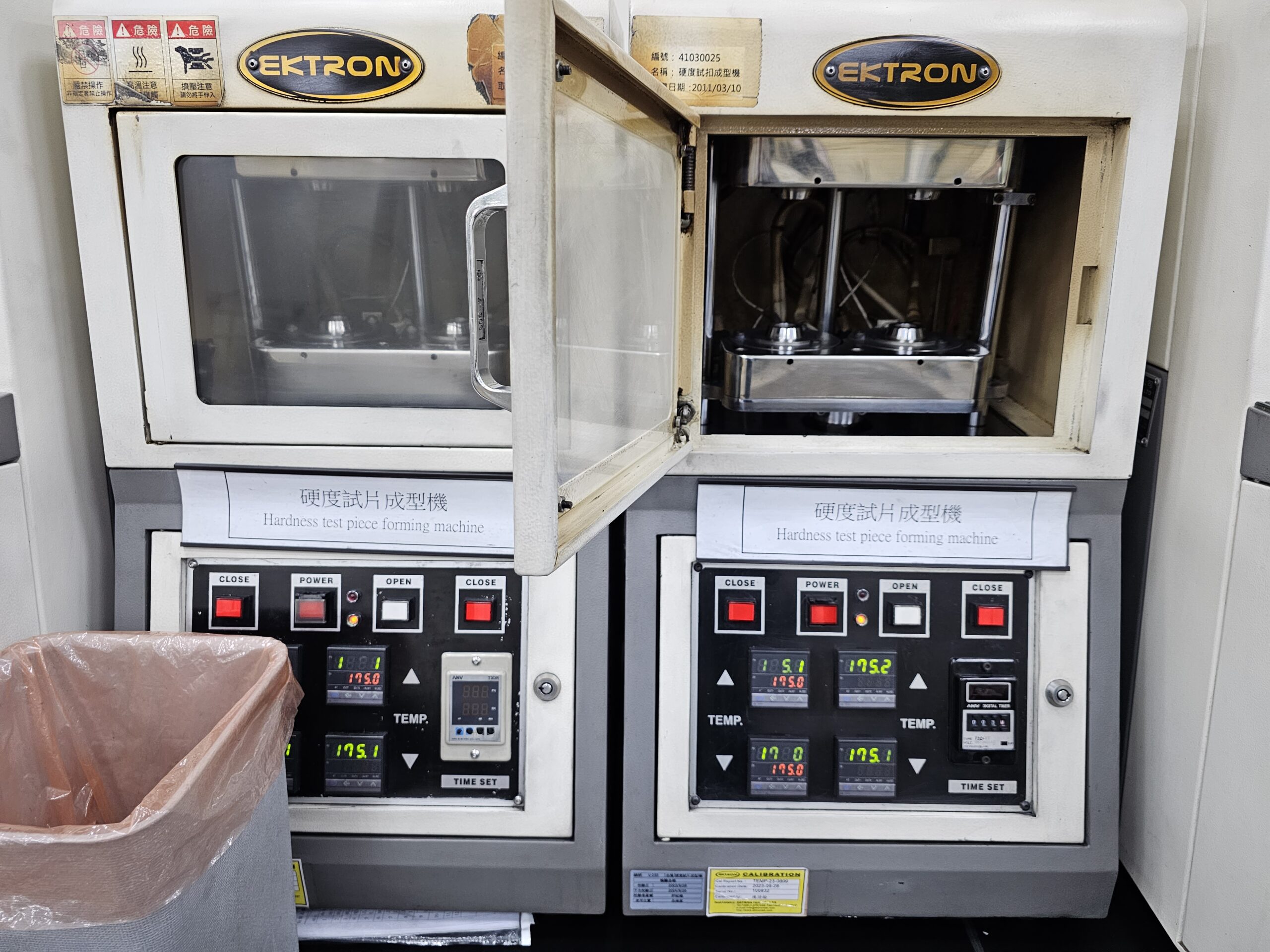
Shapes raw materials into perfect test specimens, ready for the hardness ring, ensuring accurate material strength assessments.
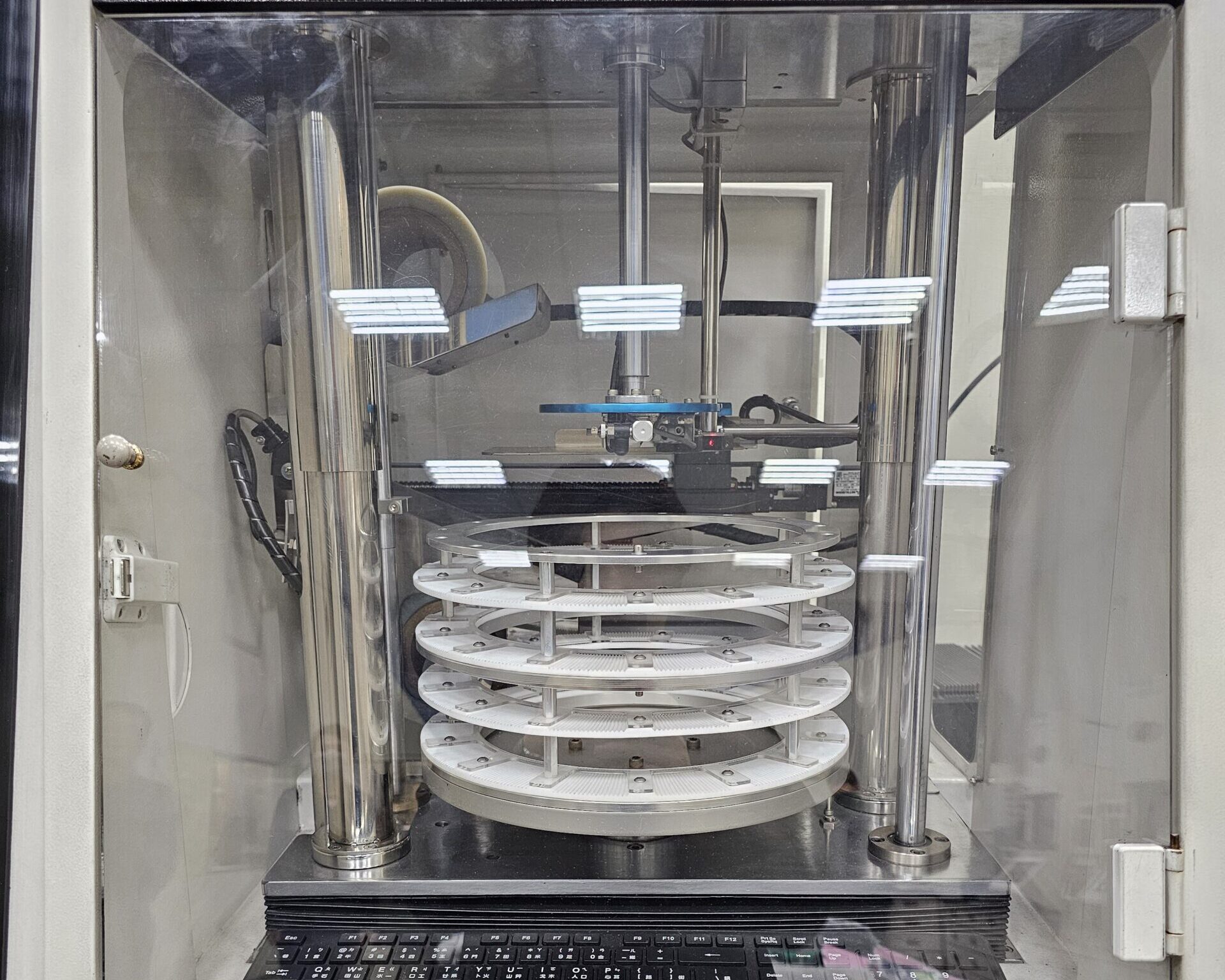
Measures the flow properties of molten polymers and other fluids at high temperatures and shear rates.
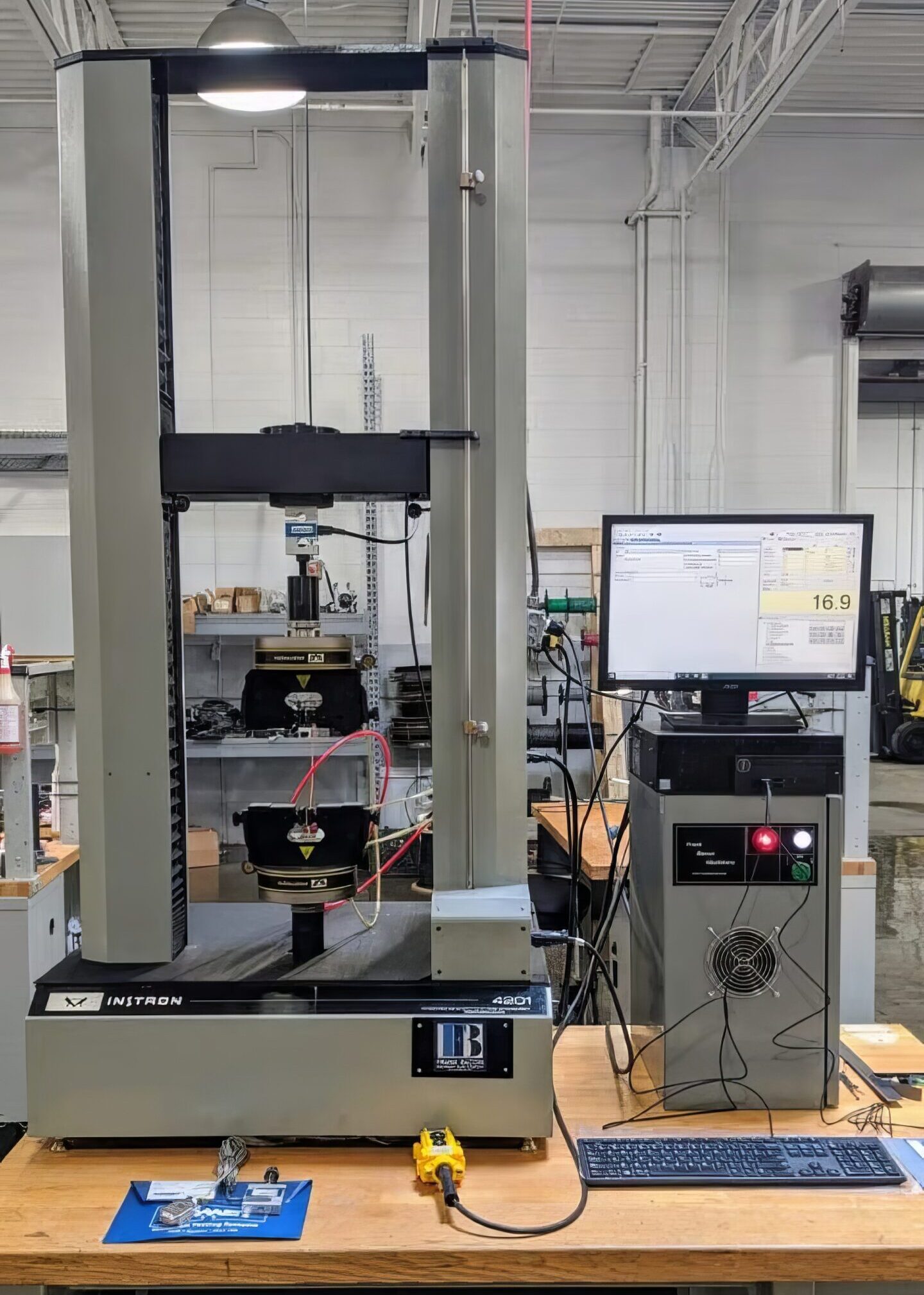
Measures material strength by applying force to stretch it, assessing properties like yield strength and elasticity.
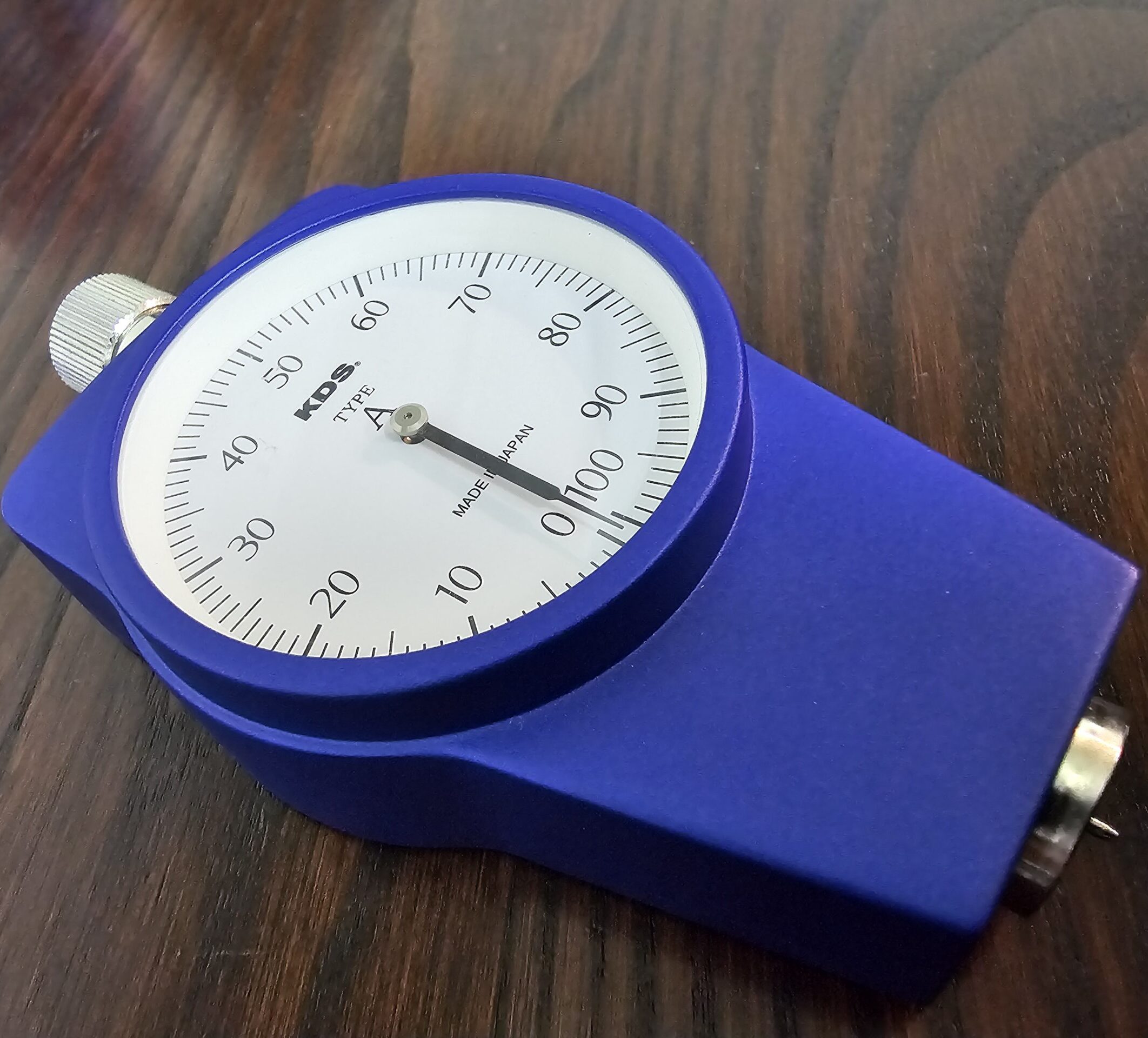
Measures material hardness by assessing its resistance to indentation. Crucial in determining material suitability for various applications.
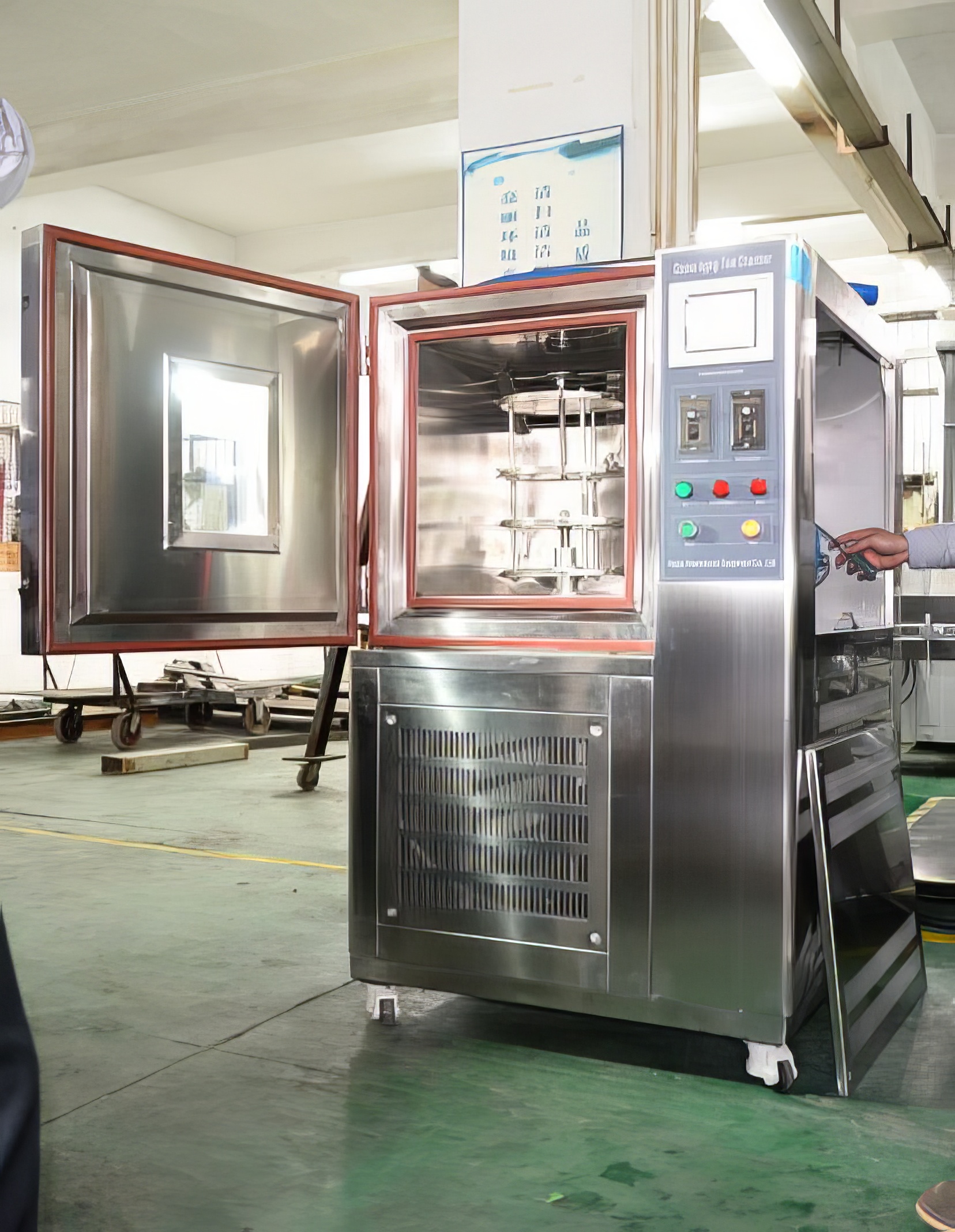
Assesses materials' resistance to ozone exposure, ensuring durability and reliability in various environmental conditions.
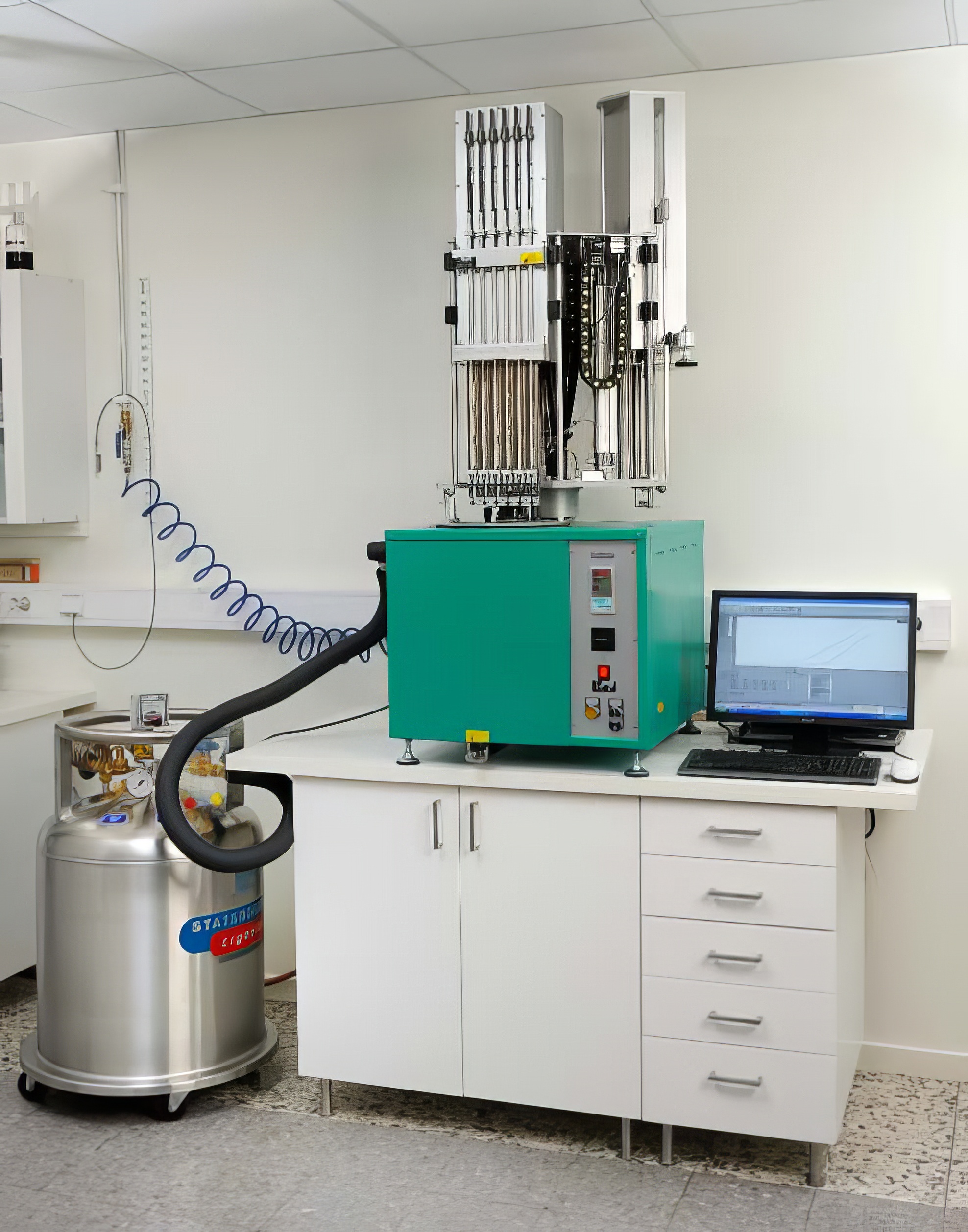
Assesses materials' susceptibility to brittleness at low temperatures, crucial for evaluating performance in cold environments.
Facilities
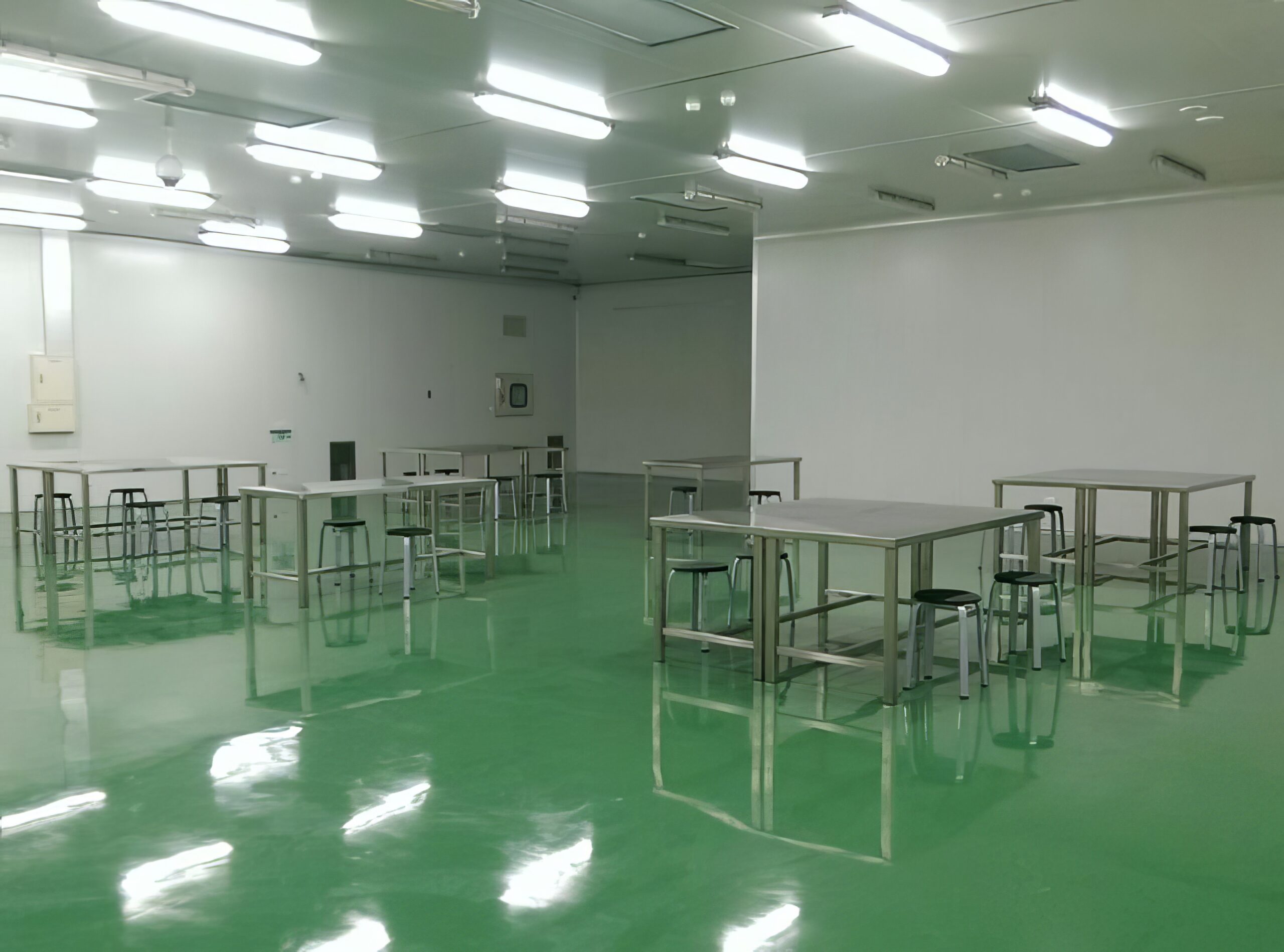
ISO Class 4 Clean Room
Maximum allowable particle count is 10,000 particles per cubic meter. Industries like pharmaceuticals, biotechnology, and aerospace often require cleanrooms of this class. They are suitable for the production of medications, medical devices, and precision electronics.
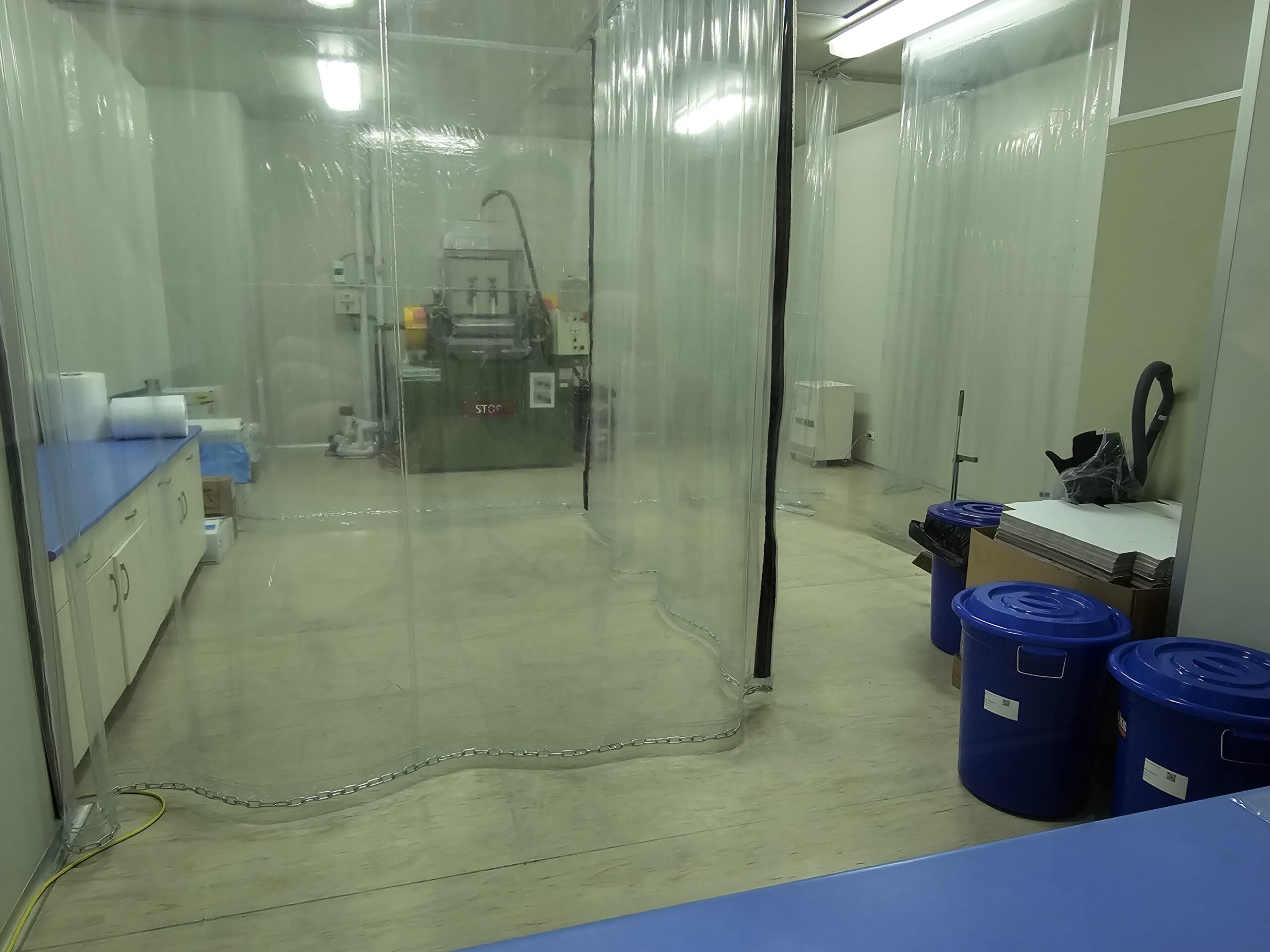
ISO Class 5 Clean Room
Maximum allowable particle count is 100,000 particles per cubic meter. Critical environments for pharmaceutical manufacturing, biotechnology, medical device manufacturing, and electronics assembly. This class is common in facilities producing sterile products.

ISO Class 6 Clean Room
Maximum allowable particle count is 1,000,000 particles per cubic meter (actually 300,000 in this particular room). Laboratories and manufacturing processes in industries such as optics, electronics, and food processing, where a controlled environment is essential to prevent contamination.
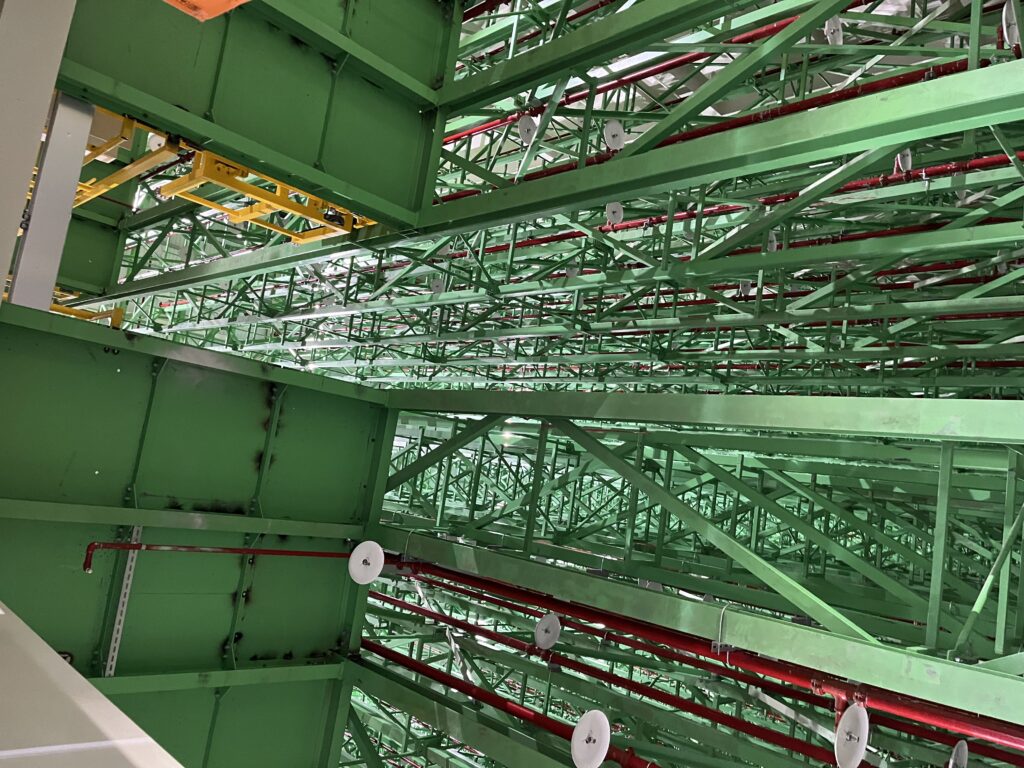
Automatic Warehouse
Products are efficiently orchestrated and transported using a state-of-the-art platform guided by an electronic interface. This dedicated space boasts a capacity of up to 2,500 palettes, 9,900 storage boxes, or 240 containers.